KingCast designs and produces zinc and aluminum permanent cast products, as well as expanding our reach to outside industries, such as transportation, energy, utility, and many others. KingCast provides a seamless flow from initial design and tooling, to cast products and powder coat finishing in-house with end-to-end machining. With all of these services fully integrated, StressCrete Group is well positioned to respond to changing customer requests, while also expanding to new and growing areas of business.
Services & Capabilities
Permanent Mold Casting
Permanent mold casting is the process of introducing molten aluminum into reusable cavities to produce superior castings. Our in-house permanent mold casting facility offers various gravity pressure casting processes to provide high-quality aluminum and zinc castings that suit every customer’s needs. Engineers provide casting design assistance, solid modeling, gating and flow analysis, plus prototyping and modeling to ensure each project is perfectly crafted to customer specifications.
Advantages
Intricate design capabilities with high dimensional precision
Castings with excellent mechanical properties
Excellent surface finish with consistent quality
Cost-effective castings due to design, tooling life and production processing
Rapid low-cost prototyping with graphite permanent molding
Design and Mold Production
With in-house mold making capabilities, our expert design team can work with you to make your concept into reality. Our experienced staff can design, engineer and manufacture tooling from scratch with the use of state-of-the-art CAD and CAM software. Conveniently, we can also alter, modify, and/or repair existing tooling.
Casting Capabilities
Our modern static and tilt-pour permanent mold facility has ten furnaces for a total capacity of 10,000 pounds, producing aluminum or zinc parts ranging from 1 ounce to 150 pounds. With a variety and various sized casting machines, our foundry allows us to operate efficiently and to deliver a wide range of high-quality castings to our customers on time.
Types
- Tilt Pour Permanent Mold – Molten metal is poured into cups while the mold is in a horizontal position and flows into the cavity as the mold is gradually tilted into a vertical position. As the molten metal flows into the mold cavity at a controlled, gradual rate, there is little turbulence present, resulting in a high-quality casting.
- Static Pour Permanent Mold – Molten metal is poured directly into the mold and fed by gravity. A fixed amount of time is given for the metal to solidify in a stationary position.
- Semi-Permanent Mold – Introducing sand cores to either tilt or static permanent methods. The use of bonded sand to produce temporary sand core inserts create desired shapes, passageways, or relieve drafts within the casting without machining for a variety of customer requirements.
- Graphite Permanent Mold Production – Excellent for smaller sized parts using a bottom fill, low turbulence process, that produces high quality, homogenous castings with an outstanding surface finish. Graphite molds are an economical option for any quantity of zinc castings or an excellent alternative for lower volumes or prototypes of aluminum castings.
Machining
Our fully equipped CNC and manual machine shop offers a variety of services including milling, turning, drilling and tapping. With the recent advancements in machine technology and CMM inspection, we can achieve tight tolerances to provide finished products that meet a variety of customer requirements.
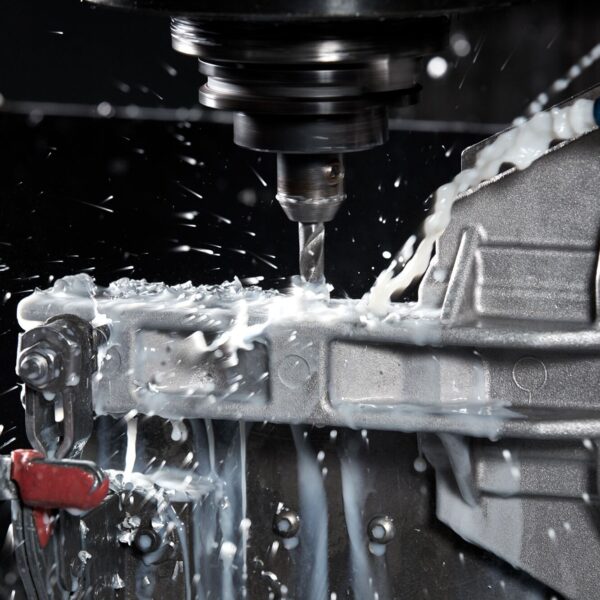
Metal Fabrication
With premium quality, efficiency and cost-effectiveness in mind, our experienced team of fabricators offer a multitude of capabilities.
- Custom and production metal fabrication
- CWB certified welding of aluminum and mild steel
- CNC HD plasma profile plate cutting capabilities for aluminum and steel
- Metal forming of pipe, plate and sheet
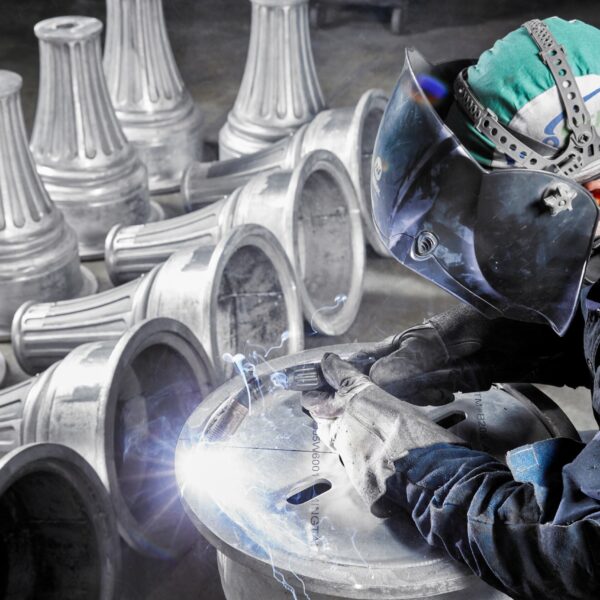
Finishing Processes
- Cutting – The process of trimming gating, excess material from a casting
- Grinding – Utilizing abrasives to remove parting lines and other excess material from a casting
- De-burring – The process of filing down unwanted edges or lines from a casting
- Shot Blasting – A process typically utilizing steel media to blast the surface of a casting, effectively cleaning and texturizing the metal
- Vibratory Finishing – Tumbling process to deburr, descale, burnish or clean and polish castings
- Heat Treatment – The process of improving the mechanical and physical properties of an aluminum casting
- Impregnation – Effectively seals against leaks and other damaging agents
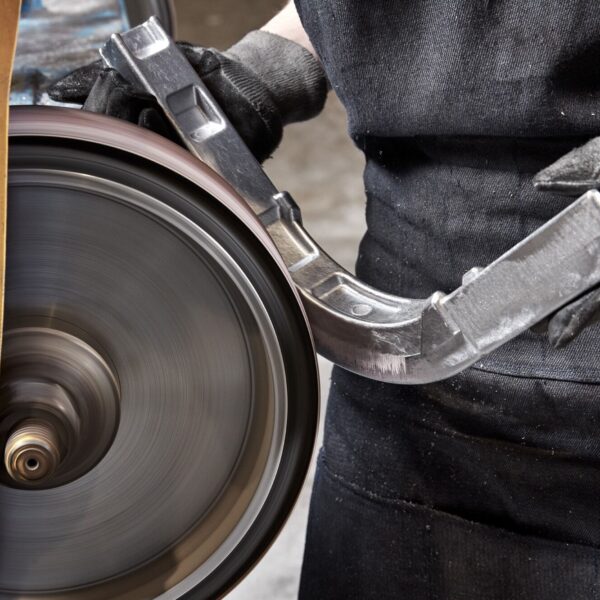